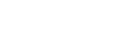
Custom Brake Details
Custom Brakes – Guidelines
by Lanner Khan
With custom brake kits in Type 1’s (T1), it is important to take into consideration and understand all the factors.
Why brake upgrades?
In my opinion, there are three reasons; brake fade, changing wheel bolt pattern and bling factor.
Brake fade is when your brakes are getting too hot and the brake compound in the pads are gassing out and no longer effective. The temperature of the brakes is exceeding the thermal properties of the friction pad. Your rotors are not cooling because they don’t get a chance to dissipate the heat between brake applications. If your brakes fade, then you need more thermal mass via larger and thicker rotors. For performance applications, vented rotors are a must. Solid rotors are for motorbikes and go-carts in my opinion. If you currently have solid rotors and are experiencing brake fade, switch to a vented rotor. If your vented rotor fades, then you need to improve the cooling or increase the thickness of your disk. Brake fade can also occur from boiling the brake fluid. This condition is not typical of street vehicles. The caliper pistons need to be insulated to prevent this, via titanium pistions or ‘pucks’ inside the existing pistons.
With brakes from other vehicles, your choice of wheels increases dramatically. The 4-130mm bolt pattern isn’t very popular with aftermarket wheel manufacturers. And let us all agree, that the wheel offerings available for the 4-130mm wheel pattern are outdated.
Got 17’s on your car? Got stock drums? Hmm…not very sexy. Big brakes behind big wheels.
Brake Hydraulics
Basic hydraulic theory states that 1) liquids are incompressible and 2) the pressure of a given closed system is the same anywhere within the system.
Pressure[P] (psi) is force [F] (lbs) over area[A] (square inches). If a 1 inch diameter piston is depressed with a force of 150lbs, this will generate a pressure of (150/3.14*.5*.5) = 190.98 psi. If a hose is connected to another piston that has a 0.5″ diameter piston we will see some force multiplication. The force would be the pressure multiplied by the piston area. (190.98psi*.25*.25*3.14)=37.50 lbs. So we see that a smaller piston will generate a smaller force given the same pressure. To summarize for a closed system:
P1= P2 (pressure 1=pressure 2)
F1/A1=F2/A2 (same as above since P=F/A)
So far so good. According to the above, just increase the piston area and you can increase the piston force for the same pressure.
If only life were so simple.
Since hydraulic theory states that liquids are incompressible, the fluid must be displaced. A displaced volume [D] is equal to a movement [M] times ares [A]. So if the same 1 inch diameter piston is depressed by 1 inch, we will displace .785 inches cube of fluid (.5*.5*3.14*1). If a second piston of .5″ diameter was connected, we would see the second piston move by 3.998 inches (.785/(.25*.25*3.14)). So, bigger pistons require more volume. To summarize for a closed system:
D1=D2 (displaced liquid 1= displaced liquid 2)
M1A1=M2A2 (movement1*area1=movement2*area2).
Understanding brake torque
Brake torque is what stops the wheels. The brake torque (ft-lbs) of a wheel is the clamping force (lbs) of the caliper times the disk radius (ft), times the coefficient of friction for the brake pad. The disk radius is measured to the centre of the brake pad.
Clamping force (lbs) is the brake line pressure (psi) times the total piston area of the caliper (square inches). The total piston area of a fixed caliper is the total of all the pistons areas. In a sliding caliper, the total piston area is the total of all the pistons times 2.
The brake line pressure (psi) is calculated from the force applied at the pedal. The pedal force (lbs) is multiplied by the pedal ratio, and divided by the master cylinder piston area (square inches).
If you’re following the story so far you will notice that rotor thickness has nothing to do with brake torque. The rotor thickness is related to the thermal capacity. Also, note that the pad area does not play a part either. Increasing the line pressure is possible by either stepping on the brake pedal harder, or decreasing the master cylinder size.
The system in action
A master cylinder is depressed which pressurizes a fluid. This pressure is transferred to the caliper pistons which in turn push the brake pad onto the disk. Adequate volume is required to insure that the master cylinder does not bottom out before the caliper can generate sufficient brake torque to stop the vehicle. The actual movement of the piston in a caliper is about 0.010″-0.015″. When the force is removed, the square seal in the caliper retracts the piston to remove the clamping force from the rotor. The above two hydraulic laws are ideal. In practice other factors must be considered; swelling of brake hoses, caliper deflections, caliper mounting deflections, compression of fluid, air inclusions in fluid etc.
Brake Bias
Also, some consideration must be paid to brake bias, that is the front to rear braking distribution. Depending on the size of your front and rear caliper pistons, you may alter the existing brake bias of your master cylinder (MC). If you understand brake torque, you will notice that rotor diameter, friction material, caliper piston size all factor into the brake bias equation. Other factors include weight distrubution of the vehicle, center of gravity of the vehicle and tire size. Weight distrubution and center of gravity factor in the dynamic weight transfer during braking. Typical rear static brake bias is only about 20-35%. Remember regardless of all the brake factors, the final word is between the tires and the pavement. With that said, you can use these factors to fine tune your vehicle’s braking characteristics.
If needed, use a proportioning valve to tame your beast. A prop valve is basically just a hydraulic pressure regulator, except that it only kicks in at a certain pressure (knee point). Up to that point, the proportioning valve does not exist (hydraulically speaking). Prop valves only reduce existing pressure. You want to set up the brake system so that under panic braking all wheels lock up the same. Then bias is SLIGHTLY to the front so that the front brakes lock up a LITTLE sooner than the rear ones. (Easier and safer to remedy understeer then oversteer in panic situations).
Depending on your brake setup, it is possible that you will have to add a prop valve to the rear circuit if you have a brake system that is biased towards the rear (rear wheels lock up before front wheels in a panic situation). Prop valves only reduce existing pressure.
Prop valves can be found at any hot rod shop. Wilwood makes a nice little unit that you can purchase directly from them. You will also need some adaptor fittings to accept metric bubble flare lines for installation. Please check local laws regarding prop valves on front circuits.